- Home
- News
- Top 6 Loading Dock Trends of 2025
Top 6 Loading Dock Trends of 2025
Since January 2024, loading dock design and operations trends have shifted in attention and priority.
Some concerns are evergreen — safety, ergonomics, supply chain integrity, etc. Others become more pronounced with changes in technology, the labor market and additional economic drivers.
What’s keeping you up at night as we begin 2025? Here are some key challenges we’re helping customers solve as we strive to make facilities safer and more productive, driving toward zero — zero safety events, zero security incidents, zero unplanned downtime and zero inefficiencies.
1. Warehouse ergonomics
This has always been important to our customers, but we’re seeing a renewed focus on ergonomics in 2025.
The aging workforce and competition for skilled labor have put ergonomics in the spotlight in just about every industry, especially in warehouses and manufacturing facilities. A major focus on physical comfort and easing strain on the job can make companies more attractive to prospective employees. Planned maintenance will ensure equipment is working as it should so operators don’t have to adjust how they interact.
Fortunately, ergonomically friendly loading dock solutions are becoming more prevalent, including hydraulic dock levelers, vertically rising powered safety gates, automatic vehicle restraints and others. These innovations are, in OSHA’s words, “helping employers fit the job to the person.”
2. Connected solutions for enhanced loading dock efficiency
In speaking with hundreds of customers about their connected facility goals, we’ve found that loading docks and doors are prime opportunities for gains in productivity, safety and uptime.
At the same time, all the data that becomes visible with connectivity can get overwhelming. Having a handle on technology to cut through the noise is critical.
A holistic, unified view of your loading dock equipment and high-speed doors backed by insights helps you make data-informed decisions and act with greater confidence. Micro-trends and other events come to light, presenting opportunities for preventative maintenance that improves productivity and uptime.
Bringing together docks, doors and interactions control into a single digital platform is the why behind Rite-Hite® ONE.
That view can then empower you to Increase productivity, maximize uptime, and help reduce safety events. With Rite-Hite ONE you can also track carrier performance and analyze equipment utilization, lower detention fees, document maintenance and uncover hidden trends to improve safety and optimize operations.
3. Warehouse and loading dock automation
Emerging technology is reshaping the way our industry loads and unloads trailers and thinks about loading dock design. With historically high traffic and increasing consumer demands, our customers need to maximize efficiency.
Automation enhances productivity by taking repetitive, mundane or strenuous tasks off employees. But it takes specialized expertise to determine the right loading dock equipment that supports automation plans for AGVs and other emerging technology.
Inside the plant, the rise in robotics in applications such as pick and place, palletizing, welding, machine tending, deburring, sawing, cutting and more, is quickly gaining momentum. Machine guarding solutions, especially automated barrier doors, are critical for enhancing safety for machine operators at the point of operation.
No matter where you are in your automation journey, considerations for incorporating automation should be part of every strategic operational decision. Rite-Hite’s automation team can help you select the right loading dock equipment to maximize your investments.
4. Drive-thru and supply chain integrity
The integrity and security of product and material transfer is a critical loading dock consideration. Semi truck theft increased sharply in 2024, with warehouses and distribution centers being the top targeted types of location.
The value of drive-thru loading dock design extends beyond theft mitigation. Loss prevention applies to maintaining environmental control and health standards for food and beverage products, including reducing product spoilage. And taking members of your loading dock team off the drive approach eliminates the possibility of back-over accidents as trailers get into position.
Combining a vertical storing leveler with a four-sided dock seal or shelter, including under-leveler seals, as part of a drive-thru dock design can help eliminate gaps where pests and contaminants can intrude — while saving energy, and maintaining supply chain integrity. Planned maintenance ensures that seals and shelters continue to keep out what you don’t want getting into your facility.
5. Safe sequence of operations
Docks are busier than ever. So turnaround times are expected to happen faster than ever.
Unfortunately, this sometimes gives workers the idea that cutting corners to save time is the right move. Paired with higher worker turnover, it’s no wonder 25% of all industrial accidents occur at the loading dock.
Programming your dock’s vehicle restraint, safety barrier, leveler and overhead door to only function in a specified, safe sequence helps prevent human error that could lead to costly outcomes. You’ll have peace of mind that your loading docks are operating efficiently and safely — and the connectivity will help identify areas for improvement. Regular service will help equipment run safely so workers don’t need to come up with workarounds.
Advanced controls like Dok-Commander® can integrate multiple pieces of loading dock equipment into one centralized panel. The goal is a safe, sequential operation tailored to fit your facility’s application.
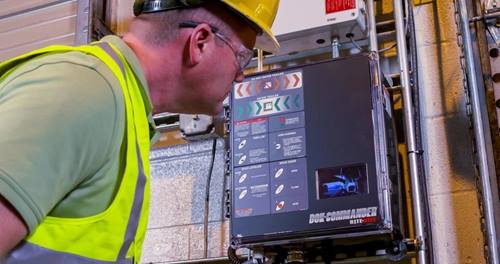
6. 24/7 safety, inside and out
Loading dock operations — the material transfer zone — extend 100′ into the facility and 100′ outside. Inherent traffic concerns cover everything from semis hauling freight to forklifts moving pallets.
Outside your facility, it’s about mitigating danger in the drive approach. Inside, you want to make communication easier and visible in high-traffic areas.
With hiring and retaining labor at a premium, prioritizing safety makes companies more attractive to potential employees and helps retention. Selecting the right hazard recognition system, vehicle restraints, safety barriers and other equipment show you’re focused on workers. Planned maintenance and proactive service of connected tools based on real-time data and trends ensures it performs safely.
Safety is paramount — the cost savings you realize while protecting employees is a bonus.
Next steps
How many of these trends hit close to home? Which solutions might benefit your organization in the short-term? And the long-term?
You don’t have to do everything all at once. Incremental change as time and budget allow always counts as progress. Still, improvements must be part of a strategic plan to improve safety and productivity, not a one-off quick fix.
There’s no one-size-fits-all solution for your challenges. If you want to talk through your circumstances with an empathetic loading dock expert, contact us for a conversation. We’ll help you identify priorities and point you toward solutions ideally suited to help meet your goals.
Find a Rep